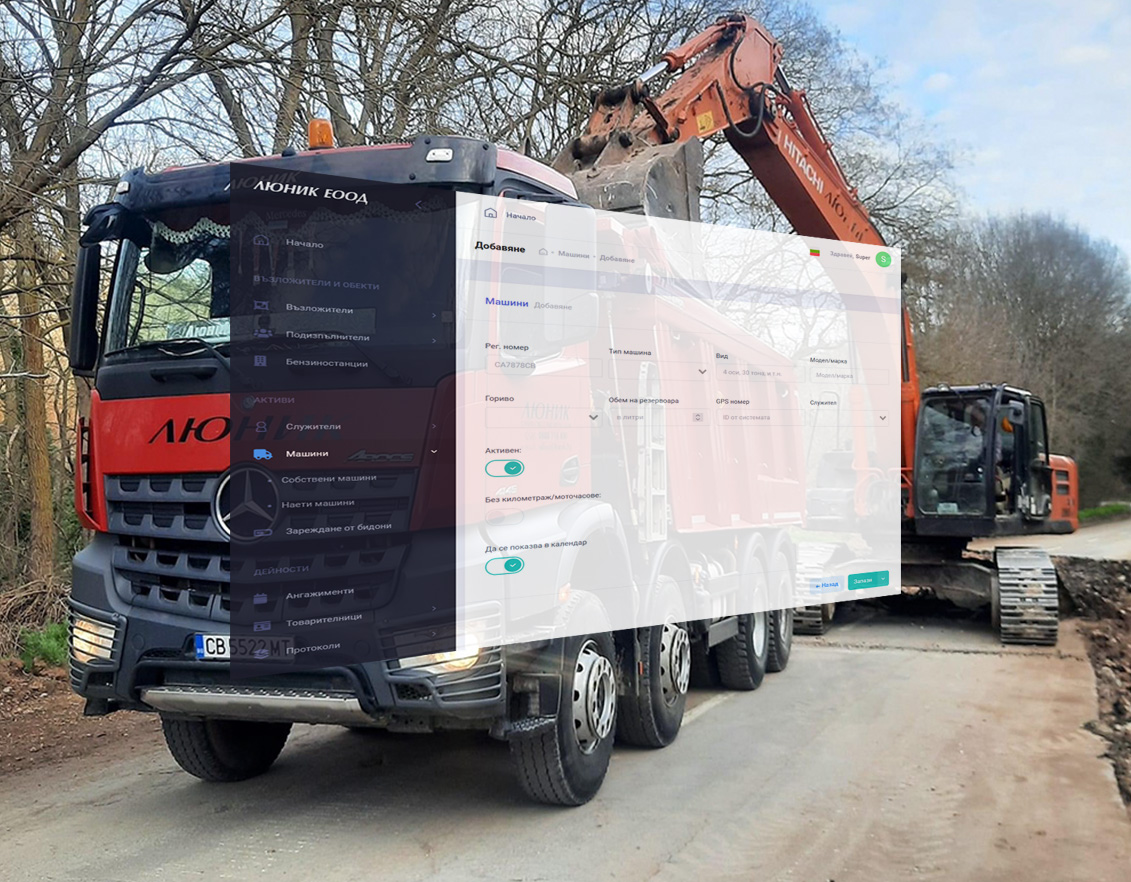
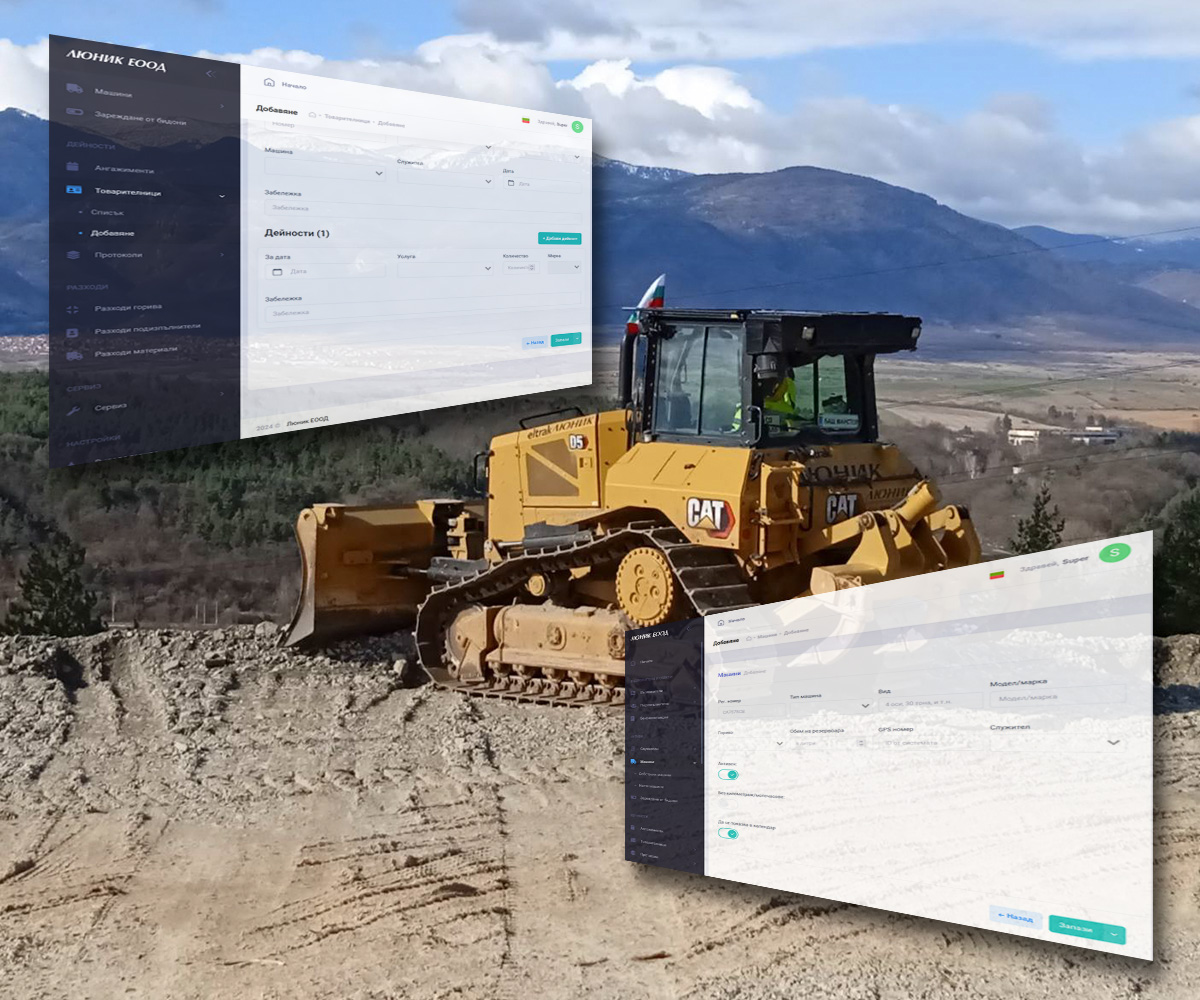
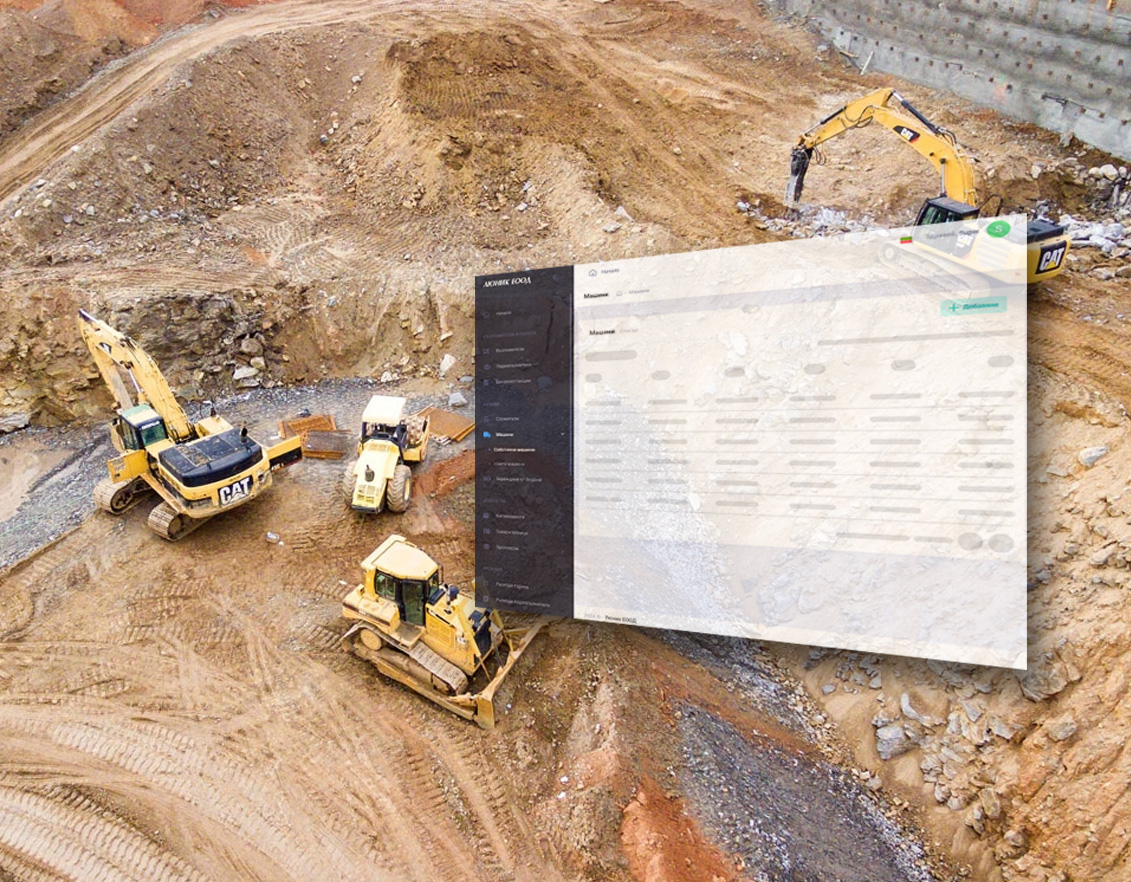
CHALLENGE
Lyunik Ltd. is an established company with decades of experience in the field of construction and transportation services performed with construction machinery. The company has hundreds of its own construction machines and sometimes uses subcontractors whose machines it also manages.
As the scale of operations grew, controlling so many units of construction equipment, associated personnel, clients, contractors, and sites became difficult. Accurate accountability and traceability of earnings and efficiency for each unit were challenging to obtain. The company needed full digitization of processes, some of which were tracked on paper, others in separate unrelated Excel spreadsheets, and others not yet defined.
SOLUTION
We created an integrated platform that tracks several processes at Lyunik:
- Planning the weekly and monthly schedules for each machine;
- Integrating data from GPS devices to monitor work performance;
- Accountability for work performed based on documents and GPS data;
- Allocating costs per client and site;
- Expenses for subcontractors and management of subcontractors’ machines;
- Creating protocols with breakdowns and recording of work done and materials used;
- Service maintenance of equipment – schedule for periodic inspections, insurances, servicing, repairs, and spare parts, with strict cost monitoring;
- Management of fuel deliveries, monitoring inventories and costs in various warehouses, refueling of machines, consumption norms, and quantity of fuel used for different activities;
- Various managerial and accounting reports showing the efficiency of work by machines, sites, clients, etc.
IMPACT
The complete digitization of the processes that we implemented in Lyunik led to significant cost optimization, better planning, higher efficiency, and predictability of the business.
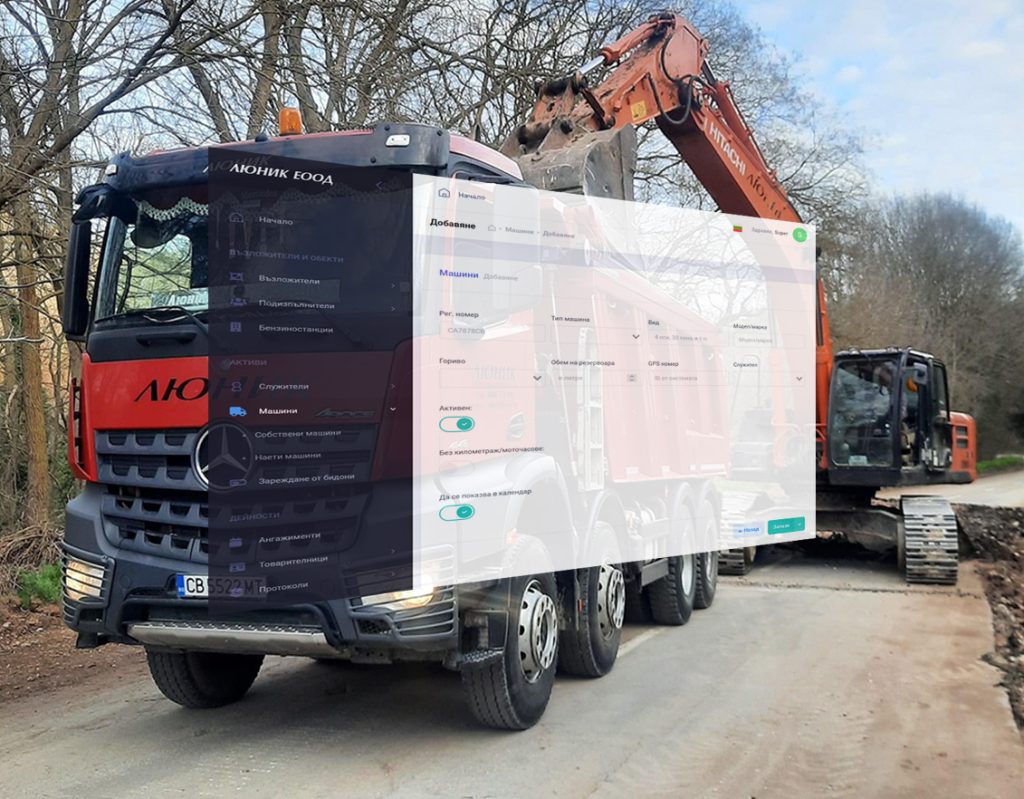
CHALLENGE
Lyunik Ltd. is an established company with decades of experience in the field of construction and transportation services performed with construction machinery. The company has hundreds of its own construction machines and sometimes uses subcontractors whose machines it also manages.
As the scale of operations grew, controlling so many units of construction equipment, associated personnel, clients, contractors, and sites became difficult. Accurate accountability and traceability of earnings and efficiency for each unit were challenging to obtain. The company needed full digitization of processes, some of which were tracked on paper, others in separate unrelated Excel spreadsheets, and others not yet defined.
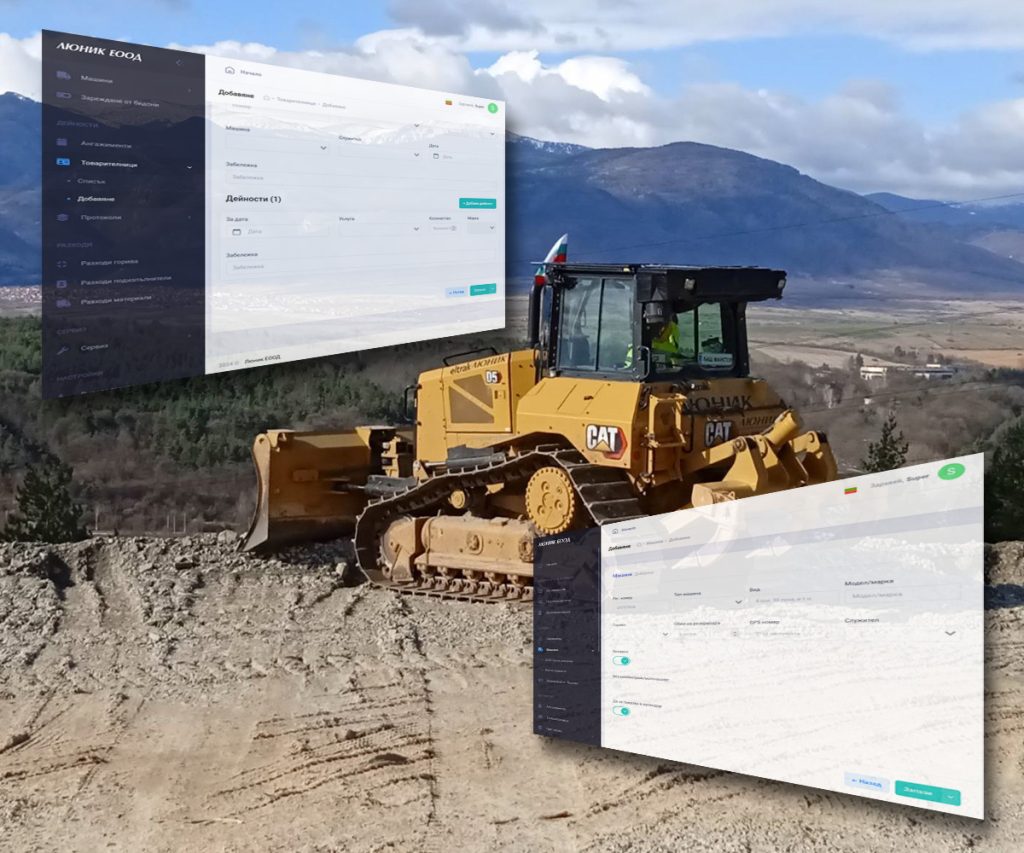
SOLUTION
We created an integrated platform that tracks several processes at Lyunik:
- Planning the weekly and monthly schedules for each machine;
- Integrating data from GPS devices to monitor work performance;
- Accountability for work performed based on documents and GPS data;
- Allocating costs per client and site;
- Expenses for subcontractors and management of subcontractors’ machines;
- Creating protocols with breakdowns and recording of work done and materials used;
- Service maintenance of equipment – schedule for periodic inspections, insurances, servicing, repairs, and spare parts, with strict cost monitoring;
- Management of fuel deliveries, monitoring inventories and costs in various warehouses, refueling of machines, consumption norms, and quantity of fuel used for different activities;
- Various managerial and accounting reports showing the efficiency of work by machines, sites, clients, etc.
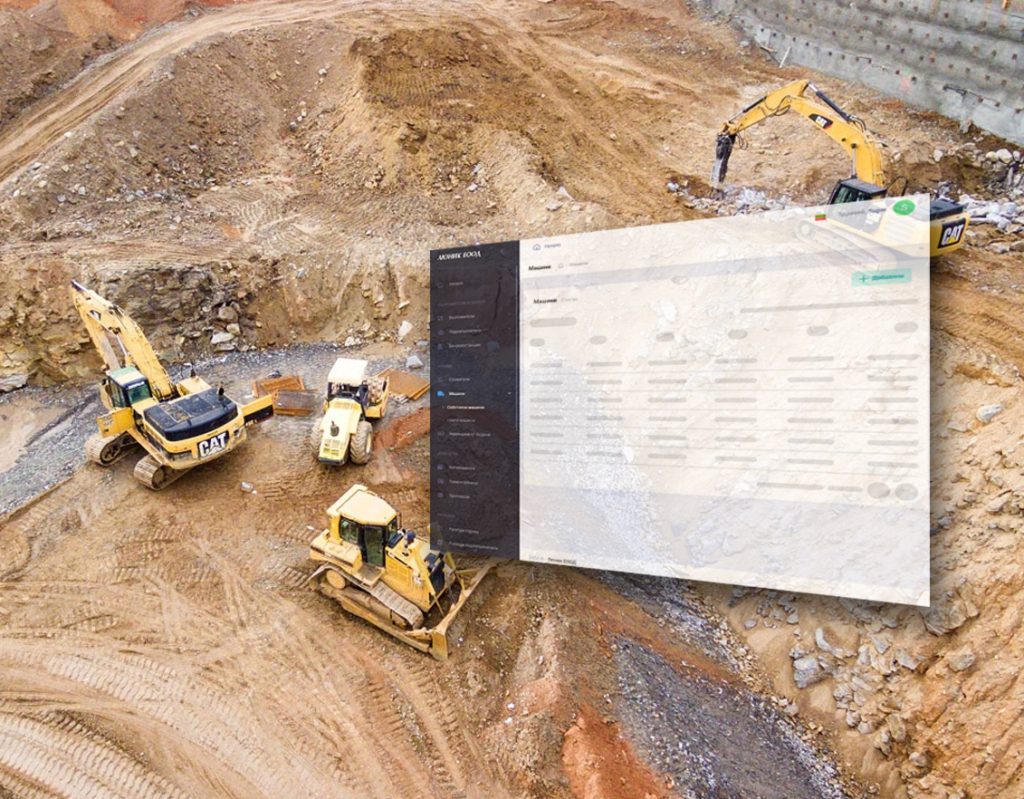
IMPACT
The complete digitization of the processes that we implemented in Lyunik led to significant cost optimization, better planning, higher efficiency, and predictability of the business.